Semi Truck Repair Near Me – Your Comprehensive Guide to Service
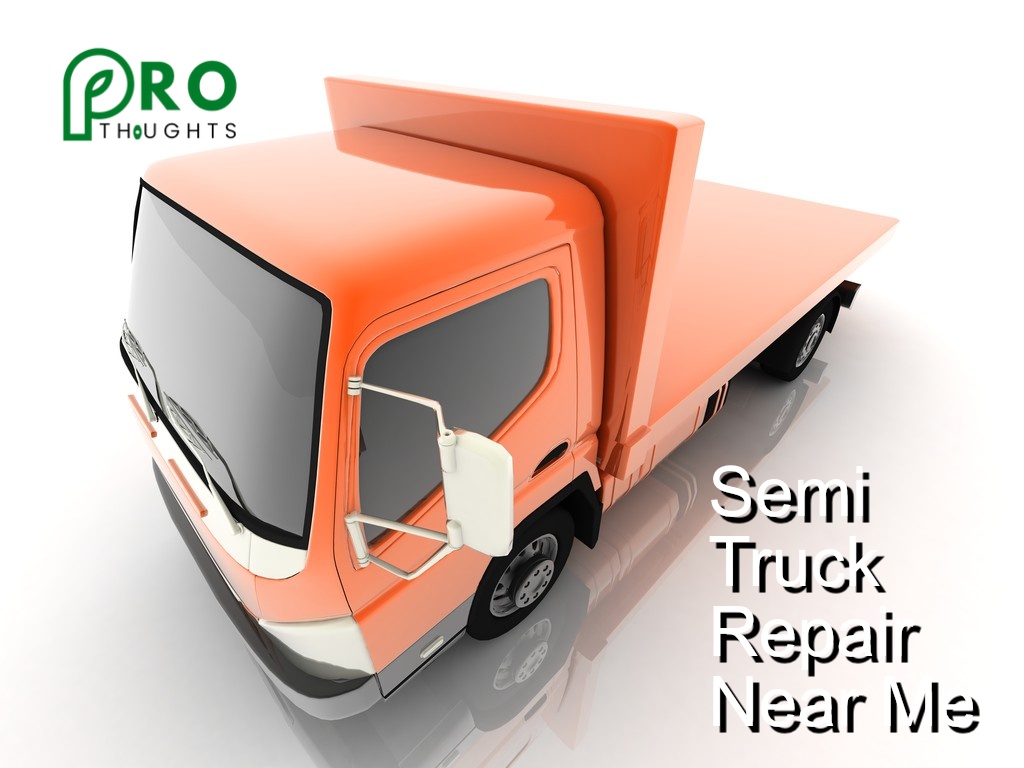
Maintaining a semi-truck is crucial for ensuring timely deliveries, minimizing downtime, and prolonging the lifespan of your fleet. Whether you own a single truck or manage a large fleet, finding reliable semi truck repair services near you is essential. This guide provides detailed insights into semi truck repair, including common issues, maintenance tips, how to choose the right repair service, and more. By understanding these aspects, you can keep your trucks in optimal condition and avoid costly repairs down the road.
Why Regular Maintenance is Essential for Semi Trucks
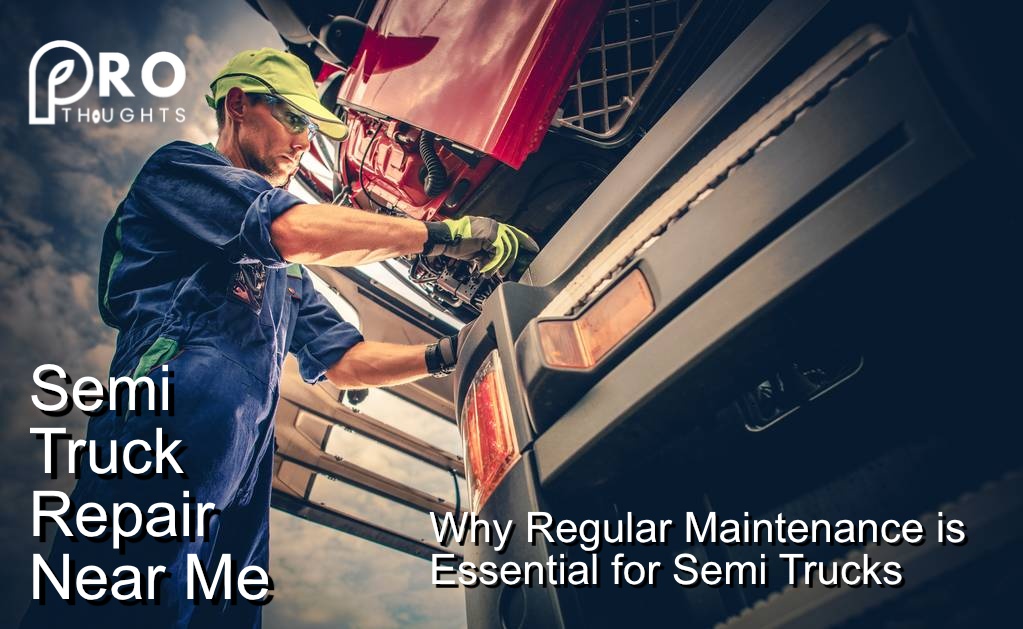
Regular maintenance is the backbone of any successful trucking operation. It helps in identifying potential issues before they become major problems, ensuring the safety of your drivers, and enhancing the overall efficiency of your fleet.
Benefits of Regular Maintenance:
- Prevents Breakdowns: Regular checks can identify and fix issues before they lead to unexpected breakdowns.
- Enhances Safety: Ensures that all truck components are functioning correctly, reducing the risk of accidents.
- Saves Money: Preventative maintenance is often less expensive than major repairs caused by neglect.
- Improves Fuel Efficiency: Well-maintained trucks consume less fuel, saving on operational costs.
- Extends Vehicle Lifespan: Regular upkeep can significantly increase the longevity of your trucks.
Common Semi Truck Problems and Their Solutions
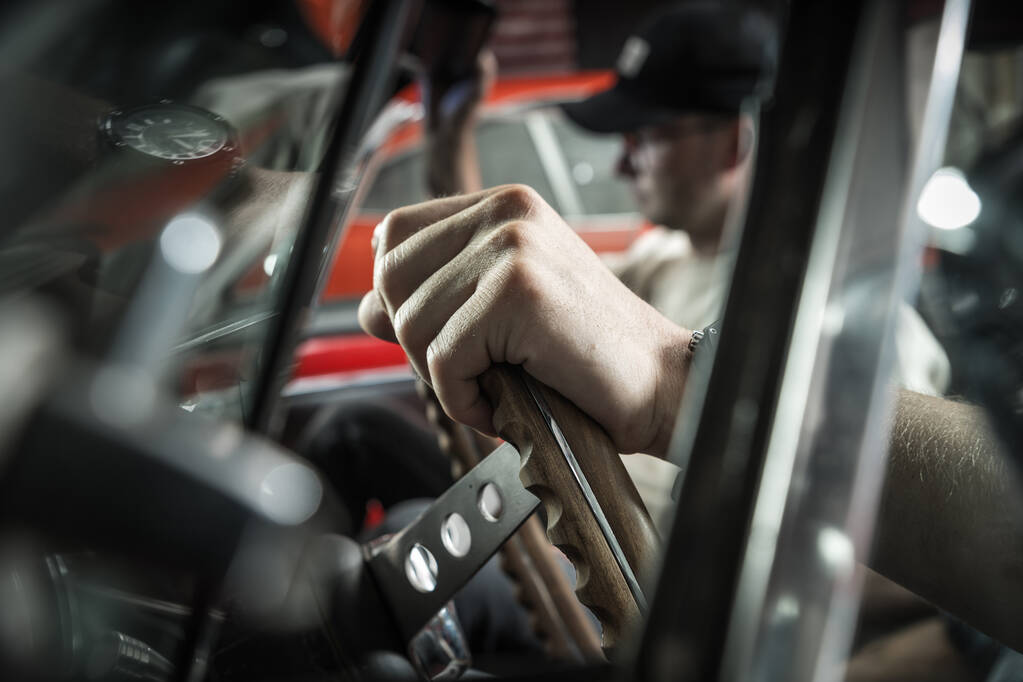
Understanding common issues that semi trucks face can help you address them promptly and effectively.
1. Engine Overheating:
- Causes: Low coolant levels, faulty thermostat, blocked radiator.
- Solutions: Regularly check coolant levels, replace faulty thermostats, and ensure the radiator is clean and free of obstructions.
2. Brake Failures:
- Causes: Worn brake pads, low brake fluid, air in brake lines.
- Solutions: Inspect and replace brake pads regularly, maintain proper brake fluid levels, and bleed brake lines to remove air.
3. Tire Blowouts:
- Causes: Underinflated tires, worn tread, debris on the road.
- Solutions: Maintain correct tire pressure, regularly inspect tire tread, and avoid roads with heavy debris.
4. Transmission Issues:
- Causes: Low transmission fluid, worn gears, faulty clutches.
- Solutions: Check and refill transmission fluid as needed, replace worn gears and clutches, and perform regular transmission inspections.
5. Electrical Problems:
- Causes: Faulty wiring, dead batteries, malfunctioning alternators.
- Solutions: Regularly inspect electrical systems, replace dead batteries promptly, and ensure alternators are functioning correctly.
Chart of Common Problems and Solutions:
Problem | Causes | Solutions |
---|---|---|
Engine Overheating | Low coolant, faulty thermostat, blockage | Check coolant, replace thermostat, clean radiator |
Brake Failures | Worn pads, low fluid, air in lines | Inspect pads, maintain fluid levels, bleed lines |
Tire Blowouts | Underinflation, worn tread, debris | Maintain pressure, inspect tread, avoid debris |
Transmission Issues | Low fluid, worn gears, faulty clutches | Refill fluid, replace gears/clutches, inspect transmission |
Electrical Problems | Faulty wiring, dead batteries, bad alternators | Inspect electrical systems, replace batteries, check alternators |
How to Choose the Right Semi Truck Repair Service Near You
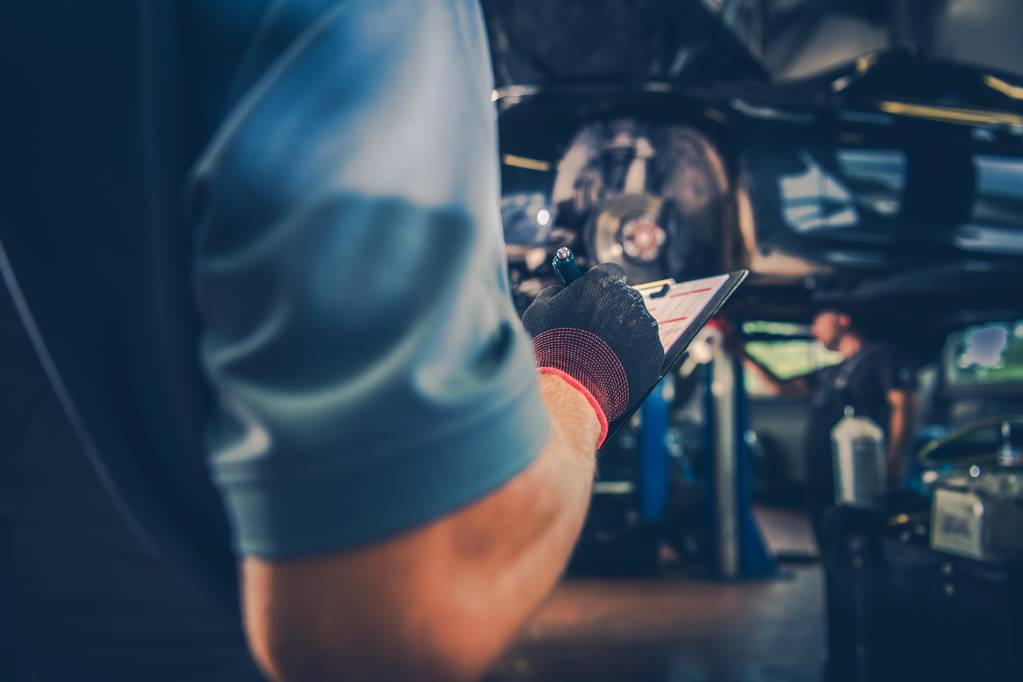
Selecting a reliable repair service is crucial for the efficient maintenance of your trucks. Here are key factors to consider when choosing a semi truck repair service near you.
1. Experience and Expertise:
- Look for Specialists: Choose repair shops that specialize in semi trucks rather than general automotive services.
- Check Certifications: Ensure that the technicians are certified and have experience with the specific makes and models of your trucks.
2. Availability and Location:
- Proximity: Select a repair service that is conveniently located to minimize downtime.
- Operating Hours: Ensure that the repair shop operates during hours that suit your schedule, including weekends if necessary.
3. Services Offered:
- Comprehensive Services: Opt for repair shops that offer a wide range of services, including engine repairs, brake services, electrical work, and tire services.
- Emergency Services: Consider repair shops that provide emergency repair services to handle unexpected breakdowns.
4. Reputation and Reviews:
- Check Online Reviews: Look for customer feedback on platforms like Google, Yelp, and industry-specific forums.
- Ask for References: Request references from other trucking companies or fleet managers who have used their services.
5. Pricing and Transparency:
- Competitive Pricing: Compare prices from different repair shops to ensure you are getting a fair deal.
- Transparent Estimates: Choose repair services that provide detailed and transparent estimates before starting any work.
6. Warranty and Guarantees:
- Service Warranty: Ensure that the repair shop offers warranties on their services and parts.
- Satisfaction Guarantee: Look for repair shops that guarantee customer satisfaction and are willing to address any issues that arise post-service.
Checklist for Choosing a Repair Service:
Factor | What to Look For |
---|---|
Experience and Expertise | Specialized in semi trucks, certified technicians |
Availability and Location | Conveniently located, flexible operating hours |
Services Offered | Comprehensive services, emergency repairs |
Reputation and Reviews | Positive online reviews, good references |
Pricing and Transparency | Competitive prices, detailed estimates |
Warranty and Guarantees | Service warranties, satisfaction guarantees |
Essential Maintenance Tips for Semi Trucks
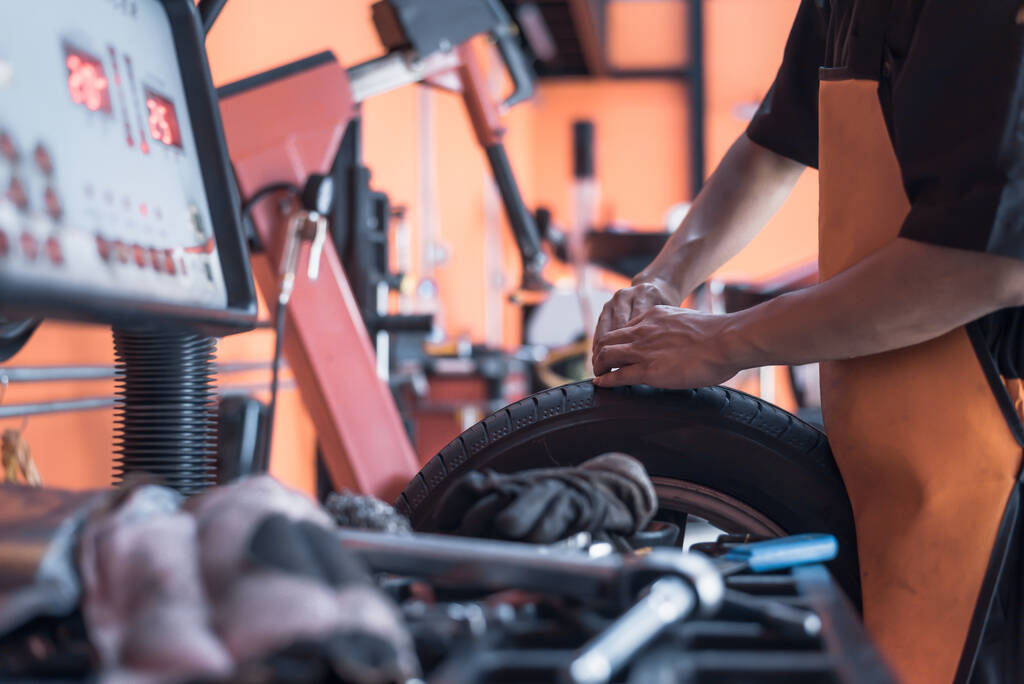
Regular maintenance is key to preventing breakdowns and ensuring the longevity of your semi trucks. Here are some essential maintenance tips to keep your fleet in top condition.
1. Regular Inspections:
- Daily Checks: Inspect tires, brakes, lights, and fluid levels before each trip.
- Weekly Inspections: Perform more thorough checks on engine components, transmission, and suspension systems.
- Monthly Inspections: Conduct detailed inspections of electrical systems, exhaust systems, and cooling systems.
2. Fluid Management:
- Engine Oil: Change engine oil and filter as per manufacturer recommendations.
- Transmission Fluid: Regularly check and replace transmission fluid to ensure smooth gear shifts.
- Brake Fluid: Maintain proper brake fluid levels and replace it periodically to prevent brake failures.
- Coolant: Keep coolant levels adequate to prevent engine overheating.
3. Tire Maintenance:
- Pressure Monitoring: Check tire pressure regularly and maintain it at recommended levels.
- Tread Inspection: Inspect tire tread for wear and replace tires when the tread is too worn.
- Rotation and Balancing: Rotate and balance tires regularly to ensure even wear and extend tire life.
4. Brake System Care:
- Brake Pads: Replace brake pads when they show signs of wear.
- Brake Lines: Inspect brake lines for leaks or damage and repair as needed.
- Brake Inspection: Have the entire brake system inspected regularly by a professional.
5. Engine Care:
- Air Filters: Replace air filters regularly to ensure proper airflow and engine efficiency.
- Fuel Filters: Change fuel filters to prevent contaminants from entering the engine.
- Cooling System: Flush and replace coolant as recommended to prevent corrosion and overheating.
6. Electrical System Maintenance:
- Battery Care: Keep batteries clean and ensure they are properly charged.
- Wiring Inspection: Regularly inspect wiring for signs of wear or damage and repair any issues promptly.
- Light Maintenance: Ensure all lights are functioning correctly and replace any burnt-out bulbs immediately.
7. Suspension and Steering:
- Suspension Components: Inspect suspension components for wear and replace them as needed.
- Steering System: Ensure the steering system is responsive and free of leaks or damage.
8. Regular Cleaning:
- Exterior Cleaning: Keep the truck clean to prevent rust and maintain a professional appearance.
- Interior Cleaning: Maintain a clean and organized cabin for driver comfort and safety.
Chart of Maintenance Tasks:
Task | Frequency | Details |
---|---|---|
Daily Checks | Every trip | Inspect tires, brakes, lights, fluid levels |
Weekly Inspections | Weekly | Check engine, transmission, suspension systems |
Monthly Inspections | Monthly | Inspect electrical, exhaust, cooling systems |
Engine Oil Change | As per manufacturer | Replace oil and filter |
Transmission Fluid | As per manufacturer | Check and replace fluid |
Brake Fluid | Periodically | Maintain and replace brake fluid |
Tire Pressure | Regularly | Check and maintain recommended pressure |
Brake Pads Replacement | When worn | Replace brake pads |
Air Filter Replacement | Regularly | Ensure proper airflow |
Fuel Filter Change | Regularly | Prevent engine contamination |
The Importance of Timely Repairs
Addressing repair needs promptly is crucial for maintaining the efficiency and safety of your semi trucks. Delaying repairs can lead to more significant issues, increased costs, and potential safety hazards.
Consequences of Delayed Repairs:
- Increased Downtime: Minor issues can escalate into major problems, resulting in extended downtime.
- Higher Repair Costs: Fixing issues early is often cheaper than addressing extensive damage caused by neglect.
- Safety Risks: Faulty brakes, tires, or engine components can compromise the safety of the driver and others on the road.
- Decreased Efficiency: Malfunctioning systems can reduce fuel efficiency and overall performance of the truck.
- Shortened Vehicle Lifespan: Continuous neglect can lead to premature wear and tear, shortening the truck’s usable life.
Tips for Managing Repairs:
- Regular Scheduling: Plan and schedule regular maintenance and inspections to catch issues early.
- Reliable Repair Partners: Build relationships with trusted repair services to ensure timely and quality repairs.
- Track Maintenance Records: Keep detailed records of all maintenance and repairs to monitor the truck’s health and schedule future services.
- Prioritize Critical Repairs: Focus on repairs that impact safety and truck functionality first.
Advanced Diagnostic Tools in Semi Truck Repair
Modern semi truck repairs leverage advanced diagnostic tools to identify and fix issues efficiently. These tools enhance the accuracy of diagnostics and reduce the time needed for repairs.
Key Diagnostic Tools:
- OBD-II Scanners: Used to read and clear diagnostic trouble codes (DTCs) from the truck’s computer system.
- Multimeters: Measure electrical values like voltage, current, and resistance to diagnose electrical issues.
- Compression Gauges: Assess the health of the engine’s cylinders by measuring compression pressure.
- Infrared Thermometers: Detect overheating components by measuring surface temperatures.
- Oscilloscopes: Analyze electrical waveforms for diagnosing complex electrical problems.
- Telematics Systems: Provide real-time data on truck performance and health, enabling proactive maintenance.
Benefits of Using Advanced Diagnostic Tools:
- Accurate Diagnostics: Precise identification of issues leads to effective and timely repairs.
- Efficiency: Reduces the time needed to diagnose problems, minimizing truck downtime.
- Cost-Effective: Prevents unnecessary repairs by accurately pinpointing the root cause of issues.
- Data-Driven Maintenance: Telematics and other data-driven tools help in planning maintenance based on actual truck usage and performance.
Chart of Diagnostic Tools and Their Uses:
Tool | Function |
---|---|
OBD-II Scanners | Read and clear diagnostic trouble codes |
Multimeters | Measure electrical values (voltage, current) |
Compression Gauges | Assess engine cylinder health |
Infrared Thermometers | Detect overheating components |
Oscilloscopes | Analyze electrical waveforms |
Telematics Systems | Provide real-time truck performance data |
Expert Insights on Semi Truck Maintenance
Gaining insights from industry experts can provide valuable perspectives on best practices and emerging trends in semi truck maintenance.
Expert Quote:
“Regular maintenance and timely repairs are not just about keeping trucks running; they’re about ensuring safety on the roads and optimizing operational efficiency. Investing in quality repair services and advanced diagnostic tools can significantly reduce downtime and costs in the long run.”
— James Carter, Fleet Maintenance Specialist
Key Takeaways from Experts:
- Proactive Maintenance: Emphasize the importance of proactive maintenance over reactive repairs.
- Training for Technicians: Ensure that repair technicians are well-trained and up-to-date with the latest technologies and repair techniques.
- Adopting Technology: Utilize advanced diagnostic tools and telematics systems to enhance maintenance strategies.
- Sustainability Practices: Incorporate eco-friendly practices in maintenance to reduce environmental impact.
How Telematics Enhances Semi Truck Maintenance
Telematics systems play a pivotal role in modern semi truck maintenance by providing real-time data and insights into truck performance and health.
Benefits of Telematics in Maintenance:
- Real-Time Monitoring: Track engine performance, fuel consumption, and other critical metrics in real time.
- Predictive Maintenance: Use data analytics to predict when maintenance is needed, preventing unexpected breakdowns.
- Route Optimization: Analyze routes to reduce wear and tear on trucks, leading to longer vehicle lifespan.
- Driver Behavior Monitoring: Assess driving habits to identify areas for improvement, enhancing safety and reducing maintenance costs.
- Asset Management: Keep track of all fleet assets, ensuring that each truck receives the necessary maintenance and repairs.
Implementing Telematics:
- Choose the Right System: Select a telematics system that fits your fleet size and specific needs.
- Integrate with Maintenance Schedules: Align telematics data with your maintenance schedules for proactive upkeep.
- Train Staff: Ensure that your maintenance team is trained to interpret and act on telematics data effectively.
- Regularly Review Data: Consistently analyze telematics data to identify trends and areas for improvement.
Chart of Telematics Benefits:
Benefit | Description |
---|---|
Real-Time Monitoring | Track performance metrics as they happen |
Predictive Maintenance | Anticipate and address maintenance needs early |
Route Optimization | Reduce unnecessary wear through efficient routing |
Driver Behavior Monitoring | Improve safety and reduce maintenance costs |
Asset Management | Efficiently manage and maintain fleet assets |
The Role of Technology in Modern Semi Truck Repairs
Technology has revolutionized the way semi truck repairs are conducted, making the process more efficient, accurate, and cost-effective.
Key Technological Advances:
- Automated Diagnostic Systems: Streamline the diagnostic process with automated tools that quickly identify issues.
- Digital Repair Manuals: Provide easy access to detailed repair instructions and diagrams.
- Mobile Repair Apps: Enable technicians to access repair information and track maintenance tasks on the go.
- 3D Printing: Allow for the on-demand production of spare parts, reducing the time needed for repairs.
- Virtual Reality (VR) Training: Offer immersive training experiences for technicians, enhancing their skills and knowledge.
Impact of Technology on Repairs:
- Increased Accuracy: Advanced tools reduce human error, ensuring precise diagnostics and repairs.
- Faster Repairs: Streamlined processes and readily available information speed up repair times.
- Cost Reduction: Efficient repairs and on-demand parts help in lowering maintenance costs.
- Enhanced Safety: Accurate repairs ensure that trucks are safe to operate, protecting drivers and others on the road.
- Improved Record-Keeping: Digital systems maintain detailed records of all repairs and maintenance activities, aiding in fleet management.
Expert Quote:
“Integrating advanced technology into semi truck repairs not only enhances the efficiency of maintenance operations but also significantly improves the accuracy of diagnostics and repairs. This leads to better-performing trucks and a more reliable fleet overall.”
— Laura Mitchell, Automotive Technology Expert
Sustainability in Semi Truck Maintenance
Sustainability is becoming increasingly important in the trucking industry. Implementing eco-friendly practices in truck maintenance can benefit both the environment and your bottom line.
Sustainable Maintenance Practices:
- Eco-Friendly Fluids: Use biodegradable and low-toxicity fluids for oil changes and other maintenance tasks.
- Recycling Parts: Recycle used parts and materials to reduce waste and lower disposal costs.
- Energy-Efficient Tools: Invest in energy-efficient diagnostic and repair tools to minimize energy consumption.
- Green Facilities: Implement energy-saving measures in your repair facilities, such as LED lighting and solar panels.
- Sustainable Disposal: Properly dispose of hazardous materials to prevent environmental contamination.
Benefits of Sustainability in Maintenance:
- Environmental Protection: Reduces the impact of maintenance activities on the environment.
- Cost Savings: Sustainable practices often lead to long-term cost savings through reduced waste and energy consumption.
- Regulatory Compliance: Helps in complying with environmental regulations and avoiding fines.
- Positive Brand Image: Demonstrates a commitment to sustainability, enhancing your company’s reputation.
Chart of Sustainable Practices:
Practice | Description |
---|---|
Eco-Friendly Fluids | Use biodegradable and low-toxicity maintenance fluids |
Recycling Parts | Recycle used parts and materials |
Energy-Efficient Tools | Invest in tools that consume less energy |
Green Facilities | Implement energy-saving measures in repair shops |
Sustainable Disposal | Properly dispose of hazardous materials |
User Tips for Implementing Sustainability:
- Audit Current Practices: Evaluate your existing maintenance practices to identify areas for improvement.
- Set Sustainability Goals: Define clear goals for reducing your environmental impact.
- Educate Your Team: Train your maintenance team on sustainable practices and their benefits.
- Partner with Green Suppliers: Source eco-friendly products and materials from reputable suppliers.
- Monitor and Report: Track your progress towards sustainability goals and report on your achievements.
Insurance and Warranty Considerations for Semi Truck Repairs
Having the right insurance and understanding warranty terms are critical aspects of managing semi truck repairs effectively.
Insurance Coverage for Repairs:
- Comprehensive Insurance: Covers a wide range of damages, including those caused by accidents, weather, and theft.
- Collision Insurance: Specifically covers damages resulting from collisions or accidents.
- Liability Insurance: Protects against claims of injury or damage caused by your trucks.
- Mechanical Breakdown Insurance: Covers repairs for mechanical failures that are not caused by accidents.
Choosing the Right Insurance:
- Assess Your Needs: Determine the level of coverage required based on your fleet size, routes, and operating conditions.
- Compare Policies: Compare different insurance policies to find the best coverage at the most affordable price.
- Understand Exclusions: Be aware of what is not covered by your insurance policy to avoid surprises during claims.
- Consult an Insurance Agent: Work with a knowledgeable insurance agent to tailor a policy that fits your specific needs.
Warranty Considerations:
- Service Guarantees: Ensure that the repair shop offers guarantees on their work, covering any defects or issues that arise after repairs.
- Parts Warranty: Check if the parts used in repairs come with a warranty, protecting you against premature failures.
- Labor Warranty: Understand the terms of labor warranties, ensuring that any issues caused by workmanship are addressed without additional costs.
- Extended Warranties: Consider purchasing extended warranties for additional coverage and peace of mind.
Chart of Insurance Types:
Insurance Type | Coverage |
---|---|
Comprehensive Insurance | Wide range of damages including weather and theft |
Collision Insurance | Damages from collisions or accidents |
Liability Insurance | Claims of injury or damage caused by trucks |
Mechanical Breakdown Insurance | Repairs for mechanical failures not caused by accidents |
Tips for Managing Insurance and Warranties:
- Review Policies Regularly: Regularly review your insurance and warranty policies to ensure they still meet your needs.
- Keep Detailed Records: Maintain detailed records of all repairs and maintenance to support insurance claims and warranty coverage.
- Understand Claim Processes: Familiarize yourself with the processes for filing insurance claims and making warranty claims to ensure swift resolution.
- Negotiate Terms: Don’t hesitate to negotiate insurance terms and warranty conditions to better suit your operational requirements.
Building a Reliable Maintenance Schedule
Creating and adhering to a reliable maintenance schedule is vital for the smooth operation of your semi trucks. A well-planned schedule ensures that all necessary maintenance tasks are performed timely, preventing potential issues and enhancing overall fleet performance.
Steps to Build an Effective Maintenance Schedule:
- Inventory of Trucks:
- List all trucks in your fleet, noting their make, model, year, and current condition.
- Identify Maintenance Tasks:
- Outline all necessary maintenance tasks for each truck, including routine inspections, fluid changes, tire rotations, and component replacements.
- Determine Frequency:
- Assign appropriate frequencies to each maintenance task based on manufacturer recommendations and usage patterns.
- Use Maintenance Software:
- Implement maintenance management software to schedule tasks, track progress, and send reminders.
- Assign Responsibilities:
- Designate specific team members or technicians responsible for each maintenance task.
- Monitor and Adjust:
- Regularly review the maintenance schedule’s effectiveness and make adjustments as needed based on truck performance and repair history.
Sample Maintenance Schedule:
Maintenance Task | Frequency | Details |
---|---|---|
Daily Inspections | Every trip | Check tires, brakes, lights, fluid levels |
Engine Oil Change | Every 5,000 miles | Replace oil and filter |
Brake Fluid Replacement | Every 10,000 miles | Maintain and replace brake fluid |
Tire Rotation | Every 7,500 miles | Rotate tires to ensure even wear |
Transmission Fluid | Every 30,000 miles | Check and replace transmission fluid |
Comprehensive Inspection | Monthly | Detailed check of engine, electrical, and more |
Battery Check | Every 15,000 miles | Inspect and test battery performance |
Tips for Maintaining the Schedule:
- Stay Consistent: Adhere strictly to the maintenance schedule to ensure all tasks are performed on time.
- Document Everything: Keep detailed records of all maintenance activities for future reference and to track truck health.
- Communicate with Drivers: Inform drivers about the maintenance schedule and ensure they report any issues promptly.
- Review Regularly: Periodically review the maintenance schedule to incorporate any changes based on truck performance and new manufacturer guidelines.
The Impact of Driver Behavior on Truck Maintenance
Driver behavior significantly affects the maintenance and longevity of semi trucks. Encouraging good driving habits can lead to reduced wear and tear, lower maintenance costs, and improved safety.
How Driver Behavior Influences Maintenance:
- Speeding: Driving at high speeds increases engine strain, tire wear, and fuel consumption.
- Harsh Braking and Acceleration: Sudden stops and starts can cause excessive wear on brakes, tires, and the engine.
- Overloading: Carrying loads beyond the truck’s capacity can stress the suspension, tires, and engine.
- Poor Route Planning: Inefficient routes lead to increased mileage, fuel usage, and exposure to road hazards.
- Neglecting Daily Checks: Failing to perform daily inspections can result in missed maintenance needs and potential breakdowns.
Tips for Promoting Good Driver Behavior:
- Training Programs: Implement training programs that emphasize safe and efficient driving practices.
- Incentive Systems: Offer incentives for drivers who consistently follow good driving habits and maintain low maintenance costs.
- Regular Feedback: Provide drivers with regular feedback on their driving performance and maintenance impact.
- Use Telematics: Utilize telematics systems to monitor driver behavior and address any issues promptly.
- Set Clear Policies: Establish and enforce clear policies regarding driving standards and maintenance responsibilities.
Chart of Driver Behaviors and Maintenance Impact:
Driver Behavior | Impact on Maintenance |
---|---|
Speeding | Increased engine strain, tire wear, higher fuel consumption |
Harsh Braking/Acceleration | Excessive brake and tire wear, engine stress |
Overloading | Stressed suspension, tires, and engine |
Poor Route Planning | Increased mileage, fuel usage, exposure to hazards |
Neglecting Daily Checks | Missed maintenance needs, potential breakdowns |
Expert Insight:
“Driver behavior plays a crucial role in truck maintenance. By fostering responsible driving habits, companies can significantly reduce maintenance costs and extend the lifespan of their fleet.”
— Laura Simmons, Fleet Management Expert
Emergency Repairs and Minimizing Downtime
Despite best efforts, emergencies can occur, leading to unexpected breakdowns and repairs. Minimizing downtime during such events is essential for maintaining operational efficiency.
Steps to Handle Emergency Repairs:
- Have a Contingency Plan:
- Develop a plan that outlines steps to take during a breakdown, including contact information for repair services and towing companies.
- Establish Relationships with Repair Shops:
- Build connections with reliable repair shops that can respond quickly to emergency repair needs.
- Equip Trucks with Essential Tools:
- Ensure that each truck carries basic tools and spare parts to handle minor repairs on the road.
- Use Telematics for Quick Diagnostics:
- Utilize telematics systems to quickly identify the issue and communicate it to repair services.
- Train Drivers on Emergency Procedures:
- Educate drivers on how to handle breakdowns, perform basic repairs, and safely secure the truck until help arrives.
Tips to Minimize Downtime:
- Regular Maintenance: Preventive maintenance reduces the likelihood of unexpected breakdowns.
- Quick Response: Ensure that repair services can respond promptly to emergencies.
- Spare Parts Inventory: Keep a stock of commonly needed spare parts to speed up repairs.
- Flexible Scheduling: Plan for flexible schedules to accommodate unexpected repairs without disrupting operations.
- Efficient Communication: Maintain clear and efficient communication channels between drivers, repair services, and fleet managers.
Chart of Emergency Repair Steps:
Step | Action |
---|---|
Contingency Planning | Outline steps and contacts for breakdowns |
Repair Shop Relationships | Connect with reliable and quick-response repair shops |
Essential Tools | Equip trucks with basic tools and spare parts |
Telematics Utilization | Use systems to diagnose and communicate issues quickly |
Driver Training | Educate drivers on emergency procedures |
Cost Management in Semi Truck Repairs
Effective cost management is essential for keeping repair expenses under control and ensuring the profitability of your trucking business.
Strategies for Managing Repair Costs:
- Preventive Maintenance: Invest in regular maintenance to prevent costly repairs caused by neglect.
- Bulk Purchasing: Buy spare parts and maintenance supplies in bulk to take advantage of discounts.
- Negotiate with Repair Shops: Negotiate prices and payment terms with repair services to get the best deals.
- Track Maintenance Expenses: Keep detailed records of all maintenance and repair costs to identify areas for cost reduction.
- Use Quality Parts: Although initial costs may be higher, using quality parts can reduce the frequency of repairs and replacements.
- Implement Fuel-Efficient Practices: Reducing fuel consumption lowers overall operational costs, indirectly impacting repair budgets.
Tips for Reducing Repair Expenses:
- Regular Inspections: Early detection of issues can prevent expensive repairs later.
- Train Drivers: Educate drivers on fuel-efficient and maintenance-friendly driving habits.
- Optimize Routes: Efficient routing reduces mileage and wear on trucks, lowering maintenance needs.
- Leverage Technology: Use maintenance management software to track and optimize repair schedules and costs.
- Evaluate Insurance Coverage: Ensure that your insurance covers essential repair costs without excessive premiums.
Chart of Cost Management Strategies:
Strategy | Description |
---|---|
Preventive Maintenance | Regular upkeep to prevent major repairs |
Bulk Purchasing | Buy supplies in bulk for discounts |
Repair Shop Negotiation | Negotiate better prices and terms |
Expense Tracking | Monitor maintenance and repair costs |
Quality Parts | Use reliable parts to reduce future repairs |
Fuel-Efficient Practices | Implement driving habits that save fuel |
Case Studies: Successful Fleet Maintenance
Learning from real-world examples can provide practical insights into effective fleet maintenance strategies.
Case Study 1: Optimizing Maintenance for a Medium Fleet
Company: FastTrack Logistics
Challenge: High maintenance costs and frequent breakdowns
Solution: Implemented a comprehensive preventive maintenance schedule, invested in telematics systems, and trained drivers on best practices
Result: Reduced maintenance costs by 20%, decreased downtime by 30%, and improved overall fleet efficiency
Case Study 2: Minimizing Downtime Through Quick Repairs
Company: RoadRunner Transport
Challenge: Frequent unexpected breakdowns causing significant delays
Solution: Established partnerships with local repair shops, equipped trucks with essential tools, and developed a robust contingency plan
Result: Minimized downtime during emergencies, maintained delivery schedules, and increased customer satisfaction
Success Story: Enhancing Fleet Longevity
Company: GreenLine Haulers
Challenge: Short lifespan of fleet trucks due to poor maintenance
Solution: Adopted a strict maintenance regimen, used high-quality parts, and monitored truck performance using advanced diagnostic tools
Result: Extended the lifespan of trucks by 15%, reduced repair frequency, and lowered overall maintenance expenses
Chart of Case Study Outcomes:
Company | Challenge | Solution | Result |
---|---|---|---|
FastTrack Logistics | High maintenance costs and breakdowns | Preventive maintenance, telematics, driver training | 20% cost reduction, 30% downtime decrease |
RoadRunner Transport | Frequent unexpected breakdowns | Repair shop partnerships, essential tools, contingency plan | Minimized downtime, maintained delivery schedules |
GreenLine Haulers | Short truck lifespan | Strict maintenance, quality parts, diagnostic tools | 15% longer lifespan, reduced repair frequency |
Expert Insight:
“Effective fleet maintenance requires a combination of proactive strategies, reliable partnerships, and continuous monitoring. By learning from successful case studies, trucking companies can implement best practices that lead to significant improvements in efficiency and cost management.”
— Daniel Harris, Fleet Management Consultant
Innovations in Semi Truck Repair
The trucking industry continually evolves, embracing innovations that enhance repair processes and fleet management.
Key Innovations:
- Automated Repair Systems: Use robotics and automation to perform repetitive and precise repair tasks, increasing efficiency and reducing human error.
- Augmented Reality (AR) for Repairs: AR technology assists technicians by overlaying digital information onto physical components, guiding them through complex repairs.
- Blockchain for Parts Tracking: Ensures the authenticity and traceability of spare parts, preventing the use of counterfeit components.
- Artificial Intelligence (AI) Diagnostics: AI systems analyze data to predict potential failures and recommend maintenance actions.
- Remote Diagnostics: Enable technicians to diagnose issues remotely, reducing the need for on-site inspections and speeding up the repair process.
Benefits of Technological Innovations:
- Enhanced Accuracy: Advanced technologies improve the precision of diagnostics and repairs.
- Increased Efficiency: Automation and remote capabilities reduce the time needed for repairs, minimizing downtime.
- Cost Savings: Efficient repair processes and the prevention of major issues lead to significant cost reductions.
- Improved Safety: Accurate and timely repairs enhance the safety of the fleet and drivers.
- Data-Driven Decisions: Access to detailed data allows for informed decision-making and strategic maintenance planning.
Chart of Innovations and Their Benefits:
Innovation | Benefit |
---|---|
Automated Repair Systems | Increased efficiency, reduced errors |
Augmented Reality (AR) | Guided repairs, improved accuracy |
Blockchain for Parts | Authenticity, traceability of parts |
AI Diagnostics | Predictive maintenance, accurate diagnostics |
Remote Diagnostics | Faster issue identification, reduced downtime |
Expert Quote:
“Embracing technological innovations in semi truck repairs not only streamlines the maintenance process but also significantly enhances the reliability and safety of the fleet. Investing in these technologies is a forward-thinking strategy that pays off in the long run.”
— Sophia Martinez, Automotive Technology Innovator
Legal and Regulatory Considerations in Truck Maintenance
Compliance with legal and regulatory requirements is essential for avoiding fines, ensuring safety, and maintaining operational legitimacy.
Key Regulations:
- Federal Motor Carrier Safety Administration (FMCSA) Standards: Guidelines for truck maintenance, driver qualifications, and safety practices.
- Environmental Regulations: Standards for emissions, waste disposal, and the use of eco-friendly fluids and parts.
- Occupational Safety and Health Administration (OSHA) Requirements: Safety protocols for maintenance facilities and technicians.
- State-Specific Laws: Varying regulations regarding truck maintenance, emissions, and safety standards across different states.
Compliance Tips:
- Stay Informed: Keep up-to-date with federal, state, and local regulations affecting truck maintenance.
- Regular Audits: Conduct regular compliance audits to ensure all maintenance practices meet legal standards.
- Train Staff: Provide ongoing training for maintenance staff on regulatory requirements and best practices.
- Document Everything: Maintain detailed records of all maintenance activities, repairs, and inspections to demonstrate compliance.
- Consult Experts: Work with legal advisors or compliance specialists to navigate complex regulations and avoid potential violations.
Chart of Key Regulations:
Regulation | Description |
---|---|
FMCSA Standards | Guidelines for truck maintenance and safety |
Environmental Regulations | Standards for emissions and waste management |
OSHA Requirements | Safety protocols for maintenance facilities |
State-Specific Laws | Varying maintenance and safety regulations by state |
Expert Insight:
“Compliance with maintenance regulations is non-negotiable in the trucking industry. It not only ensures the safety of your fleet but also protects your business from legal repercussions and financial penalties.”
— Michael Thompson, Transportation Compliance Officer
The Future of Semi Truck Maintenance
As the trucking industry evolves, so does the approach to maintenance. Future trends are set to revolutionize how semi truck maintenance is conducted, making it more efficient, sustainable, and technologically advanced.
Emerging Trends:
- Electric and Hybrid Trucks: As electric and hybrid trucks become more prevalent, maintenance practices will shift towards specialized care for electric drivetrains and battery systems.
- Predictive Analytics: Leveraging big data and machine learning to predict maintenance needs and prevent issues before they occur.
- Connected Maintenance Networks: Creating interconnected networks of repair services and maintenance facilities for seamless service delivery.
- Sustainable Practices: Increasing emphasis on eco-friendly maintenance practices to reduce the environmental impact of trucking operations.
- Advanced Training Programs: Utilizing virtual reality and simulation technologies to train maintenance technicians more effectively.
Impact of Future Trends:
- Improved Efficiency: Advanced technologies and predictive analytics will streamline maintenance processes, reducing downtime and costs.
- Enhanced Sustainability: Eco-friendly practices and the rise of electric trucks will lead to greener trucking operations.
- Better Fleet Management: Connected maintenance networks and real-time data will enable more effective fleet management and strategic decision-making.
- Skilled Workforce: Advanced training programs will produce highly skilled technicians capable of handling the complexities of modern and future truck technologies.
Chart of Future Trends and Their Impact:
Trend | Impact |
---|---|
Electric and Hybrid Trucks | Specialized maintenance for electric systems |
Predictive Analytics | Preventative maintenance, reduced downtime |
Connected Maintenance Networks | Seamless service delivery, improved fleet management |
Sustainable Practices | Reduced environmental impact, cost savings |
Advanced Training Programs | Highly skilled maintenance workforce |
Expert Quote:
“The future of semi truck maintenance lies in the integration of advanced technologies and sustainable practices. Embracing these changes will not only enhance operational efficiency but also contribute to a more environmentally responsible trucking industry.”
— Dr. Karen Lee, Transportation Technology Futurist
Conclusion
Maintaining semi trucks is a complex but essential aspect of the trucking industry. By understanding common problems, implementing regular maintenance schedules, leveraging advanced diagnostic tools, and staying compliant with regulations, you can ensure that your fleet operates smoothly and efficiently. Building strong relationships with reliable repair services, adopting sustainable practices, and embracing technological innovations will further enhance your maintenance strategy, leading to reduced costs, increased safety, and prolonged vehicle lifespans. As the industry continues to evolve, staying informed and adaptable will be key to maintaining a successful and resilient trucking operation.
Frequently Asked Questions (FAQs)
1. What are the most common maintenance issues in semi trucks?
The most common maintenance issues in semi trucks include engine overheating, brake failures, tire blowouts, transmission problems, and electrical issues. Regular inspections and timely repairs can prevent these problems from escalating.
2. How often should I perform maintenance on my semi trucks?
Maintenance frequency depends on the truck’s usage and manufacturer recommendations. Generally, daily inspections before each trip, weekly checks, monthly inspections, and scheduled major maintenance based on mileage are recommended.
3. What should I look for when choosing a semi truck repair service near me?
When choosing a repair service, consider their experience and expertise, availability and location, range of services offered, reputation and reviews, pricing transparency, and the warranties they provide on their work.
4. How can telematics systems help in maintaining my semi trucks?
Telematics systems provide real-time data on truck performance, enabling predictive maintenance, route optimization, driver behavior monitoring, and overall fleet management, which helps in reducing downtime and maintenance costs.
5. What are the benefits of preventive maintenance for semi trucks?
Preventive maintenance helps prevent unexpected breakdowns, enhance safety, save money on costly repairs, improve fuel efficiency, and extend the lifespan of your trucks.